Opening the Power of Welding WPS: Methods for Efficiency and Safety in Manufacture
In the world of manufacture, Welding Treatment Specs (WPS) stand as the foundation of welding operations, determining the required steps for attaining both efficiency and safety and security in the fabrication procedure. Understanding the details of WPS is vital to harnessing its complete capacity, yet numerous organizations battle to open real power that exists within these papers (welding WPS). By delving right into the approaches that enhance welding WPS, a world of boosted performance and heightened security waits for those prepared to discover the nuances of this essential aspect of construction

Value of Welding WPS
The value of Welding Treatment Specifications (WPS) in the construction sector can not be overstated. WPS act as a crucial roadmap that lays out the necessary steps to guarantee welds are performed constantly and correctly. By defining crucial parameters such as welding processes, materials, joint styles, preheat temperature levels, interpass temperature levels, filler steels, and post-weld heat treatment requirements, WPS offer a standard approach to welding that boosts efficiency, quality, and safety in fabrication processes.
Adherence to WPS aids in achieving uniformity in weld high quality, reducing the possibility of flaws or structural failures. This standardization also promotes compliance with sector regulations and codes, making sure that produced frameworks meet the needed safety and security standards. Additionally, WPS paperwork makes it possible for welders to reproduce successful welding procedures, bring about constant outcomes across different jobs.
Basically, the meticulous growth and strict adherence to Welding Treatment Specs are vital for promoting the integrity of welded frameworks, guarding versus possible dangers, and maintaining the track record of manufacture companies for delivering premium items and solutions.
Crucial Element of Welding WPS
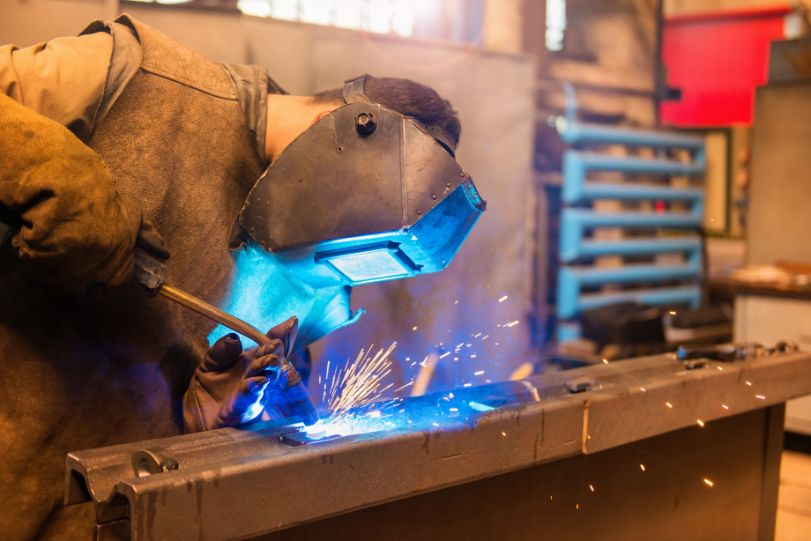
Enhancing Performance With WPS
When optimizing welding operations, leveraging the essential aspects laid out in Welding Treatment Requirements (WPS) becomes important for improving processes and optimizing productivity. One way to enhance efficiency with WPS is by carefully selecting the appropriate welding parameters.
Consistently examining and updating the WPS to include any type of lessons learned or technical developments here can additionally contribute to efficiency enhancements in welding operations. By accepting the guidelines established forth in the WPS and continuously looking for ways to maximize processes, makers can achieve greater performance levels and exceptional end outcomes.
Ensuring Safety in Manufacture

Safety protocols in fabrication play a pivotal role in protecting personnel and optimizing operational treatments. Ensuring safety and security in manufacture entails a complex technique that encompasses numerous aspects of the welding process. One essential aspect is the provision of individual safety devices (PPE) tailored to the details threats existing in the fabrication setting. Welders must be outfitted with suitable gear such as helmets, handwear more covers, and safety clothes to mitigate threats linked with welding activities.
In addition, adherence to appropriate air flow and fume extraction systems is critical in keeping a healthy job atmosphere. Welding fumes contain damaging substances that, if breathed in, can position severe health and wellness risks. Carrying out reliable ventilation steps aids to decrease direct exposure to these harmful fumes, promoting respiratory health among employees.
Routine tools maintenance and examinations are also crucial for guaranteeing safety and security in fabrication. Malfunctioning equipment can address result in crashes and injuries, highlighting the relevance of routine checks and timely fixings. By focusing on precaution and cultivating a society of awareness, construction centers can develop a secure and efficient workplace for their workers.
Carrying Out WPS Ideal Practices
To enhance functional efficiency and make sure quality end results in construction procedures, integrating Welding Treatment Spec (WPS) ideal methods is paramount. Choosing the appropriate welding procedure, filler product, and preheat temperature level defined in the WPS is critical for attaining the desired weld quality. Ensuring that qualified welders with the necessary certifications carry out the welding procedures according to the WPS guidelines is essential for consistency and integrity.
Conclusion
To conclude, welding WPS plays an essential function in ensuring effectiveness and safety and security in fabrication processes. By concentrating on crucial elements, boosting efficiency, and executing best practices, firms can maximize their welding procedures. It is necessary to focus on precaution to stop crashes and ensure a smooth manufacturing process. By adhering to these strategies, services can open the complete capacity of welding WPS in their fabrication procedures.
In the realm of fabrication, Welding Procedure Specifications (WPS) stand as the foundation of welding operations, determining the needed steps for attaining both efficiency and security in the manufacture procedure. By specifying important parameters such as welding procedures, materials, joint designs, preheat temperature levels, interpass temperature levels, filler steels, and post-weld warm treatment demands, WPS offer a standardized approach to welding that boosts performance, high quality, and security in fabrication processes.

When enhancing welding procedures, leveraging the vital components outlined in Welding Procedure Specs (WPS) comes to be essential for improving processes and making best use of productivity. (welding WPS)